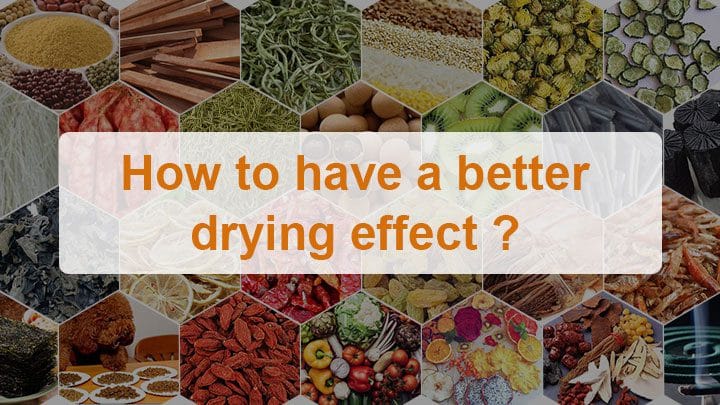
The essence of material drying is to remove the moisture in the material. What are the factors that affect the removal of moisture? How can we make the material drying better and more evenly dried? Next, I will tell you some factors that will affect the drying effect during the drying process.
Temperature
The main function of temperature is to evaporate the water inside the material. Generally speaking, the higher the temperature of the hot air, the higher the heat transfer rate and mass transfer rate. The greater the temperature difference between the heat transfer medium and the material, the greater the rate of heat transfer to the material. However, different materials require different drying temperatures, so the temperature cannot be raised blindly for the following reasons.
- First of all, for some soft and juicy raw materials, the swelling of the juice will cause the skin to rupture due to the high temperature, which will affect the quality of drying.
- In the case of high temperature and low humidity, the material is prone to encrustation, resulting in insufficient drying of the inside of the material.
- For some materials with high sugar content, high temperature can easily cause sugar coking.
The increase of the temperature of the medium should be based on the principle of not damaging the quality requirements of the finished product. Choosing a suitable temperature can improve the drying efficiency on the one hand, and on the other hand, it can ensure the shape and color of the finished product after drying.
Wind speed
The main effect of wind speed is to continuously transfer heat to the material and take away the saturated water vapor around the material. The flow rate of the hot air affects the heat transfer during the drying process. Generally speaking, the higher the wind speed of the hot air, the higher the drying rate, especially in the initial stage of drying.
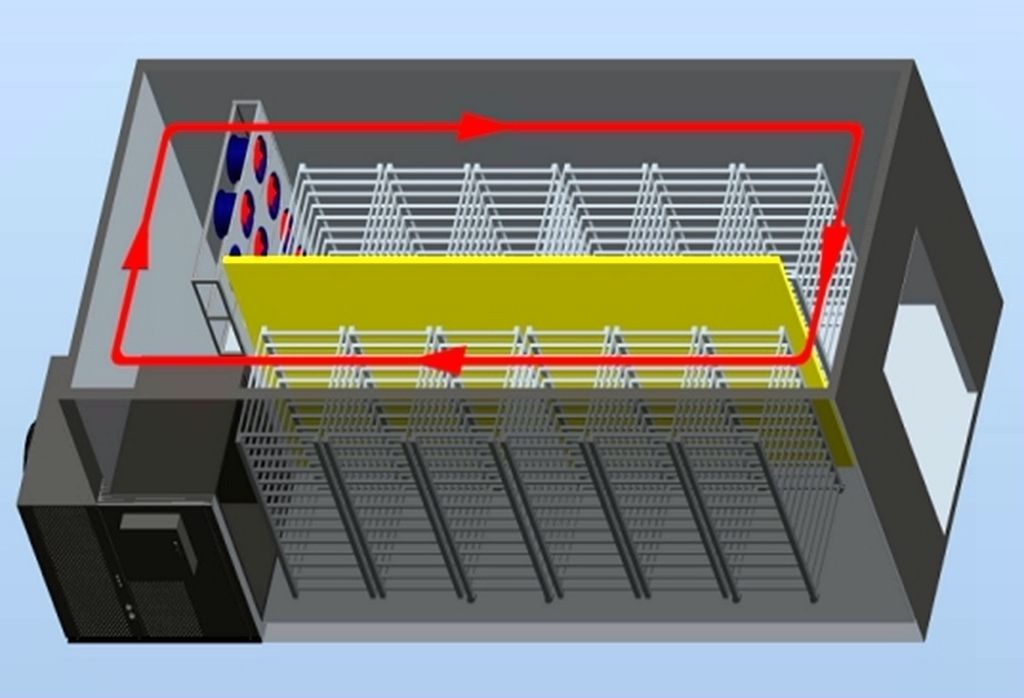
For the hot air circulation dryer, sufficient air volume can ensure the complete circulation of the hot air inside the dryer. Increasing the wind speed of the hot air directly increases the heat transfer coefficient and increases the drying rate.
The hot air can be replaced in time as the wind speed increases, ensuring the circulation of the hot air. However, for the increase of the hot airspeed, for a certain length of the dryer, the residence time of the hot air inside the dryer will be reduced, which may cause a waste of heat energy and affect the thermal efficiency.
Humidity
The lower the relative humidity of the air in the drying room, the faster the water will flow out of the material. In the initial stage of drying, this effect is particularly significant. The ability of wet air that is close to saturation to further absorb moisture is far worse than that of dry air and the saturated humid air can no longer absorb the evaporated moisture from the material.
The structure and properties of the material
This mainly includes the physical structure, chemical composition, shape and size of the material, the thickness of the material layer and the way of internal moisture binding. The structure and nature of the material are different, and the way it combines with moisture is different. When dried under the same conditions, the drying rate is different.
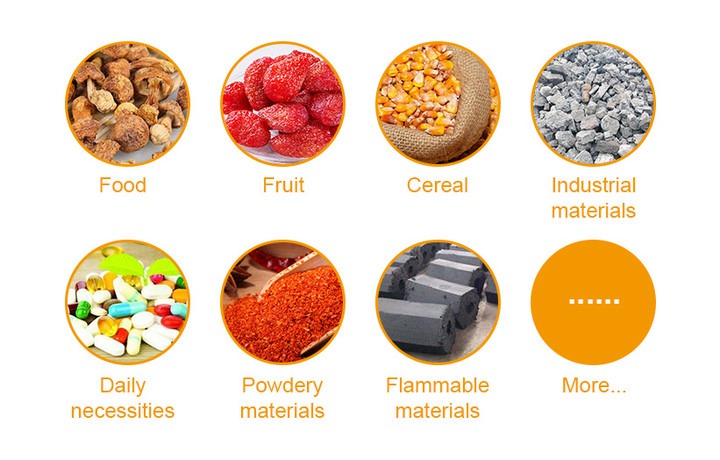
The material forms mainly include strips, blocks, flakes, powder, etc. Generally speaking, the drying efficiency of flake materials is faster, and the drying efficiency of block or rhizome is slower. The shape of the material determines the way the material is placed and the design of the air duct.
Placement and contact of materials
In the case of a certain drying rate, the larger the contact area between the material and the hot air, the better the overall drying effect. When the hot airflow direction is perpendicular to the vaporization surface of the material, the drying speed is the fastest, and when they are parallel to each other, the drying speed is the lowest.